

Circular Economy
Today, Cutting Edges is a company that focuses most of its attention on the entire supply chain involved in production activities, processes and services.
Over the years, many interventions have been dedicated to the study of the logics of industrial development modeled by the competent bodies of the European Union and National Public Institutions.
Through this study it has been realized the construction of numerous alliances with private companies, Public Institutions, Participated and Third Sector.
All this is placing our reality at the center of a Innovation Hub aimed primarily at the "construction" of a Circular Economy functional to the common benefit, innovative, economic, humanistic and, not least, of universal collaboration.
The Circular Economy is today a fundamental subject for one of the most discussed topics concerning the correct relationship between profit, environment and community.


LEFTOVERS AND SUSTAINABLE DIE-CUTTING
During the production phases, up to 30% of the raw material can be left over, to ensure durability and very high performance, the dies must be made to perfection. During the die-cutting phase, the stresses reach up to 10,000 strokes per hour and the average life of a die (several years) is approximately 2.5-3 million strokes. This almost obligatory processing system generates significant waste, in the past only Cutting Edges produced approximately 35 tons of wood per year destined for landfill. This condition is common to all die-cutting manufacturers who today have no possibility of recovering the raw material.
THE REVOLUTIONARY RECOVERY WITH LASER CUTTING
Thanks to its R&D and experimentation office, Cutting Edges has patented a system for the recovery of waste during the laser cutting phase.
By exploiting the characteristics of the main material (wood), its exclusive properties (fireproof and planar) and using the available technology (laser), he created a system for the use of waste.
The objects to be produced are broken down into universal pieces (similar to a puzzle) and with the help of specific software (Nesting) they are positioned in the leftovers of the panel to be cut. After cutting they are assembled to generate new panels, products or parts of furniture. This operation is only possible because the centesimal precision of the laser cutting, combined with the calibration of the wood, guarantee a perfect fit, favoring the direct passage to the finishing phase.

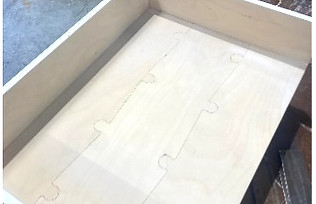
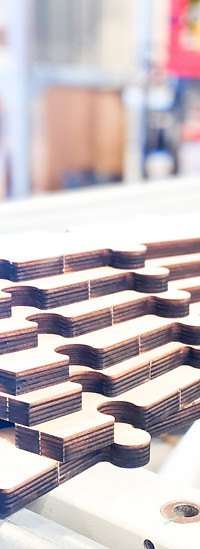
RECYCLING IS NOT SUSTAINABLE


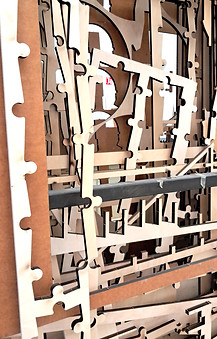
This new working methodology offers the possibility of creating any type of object of shape and size with a precision that today the carpentry market cannot offer. Examples of objects already made, key rings, lamps, seats, components for kitchens, bedrooms, bathroom furniture, indoor and outdoor tables, drawers, etc.
Inside the production area of Cutting Edges, a space of approximately 400 m2 has been created where a carpentry shop has been created. These machines allow the object to be tested and the relative industrialisation process to be evaluated. This direct processing guarantees the possibility of certifying each object as SUSTAINABLE.
The possibility of certifying our products as sustainable is given by the fact that we “recover” the wood during the production phase, not using virgin panels but only scraps. Unlike recycled panels that are composed of the recruitment of wood identified as “waste”, our process does NOT imply the use of resources, of processing for transformation, does not use glue and does not release emissions into the atmosphere. A slogan could be:
Recycling is NOT Sustainable, Recovering IS.
HIMADE – HUB IDEA MADE IN ITALY
The Himade brand, in conjunction with Cutting Edges, will replicate the business model across all die manufacturers, leasing the nesting program to optimize laser cutting operations. This system will improve production efficiency, reducing material waste that is currently managed as waste. In addition, Himade will offer a rebate for cutting universal parts, providing a direct economic benefit to die makers. The process will also help improve the overall sustainability of operations, ensuring higher scores in ESG certifications, thus strengthening their environmental and social reputation.
Visit the link: www.himade.it
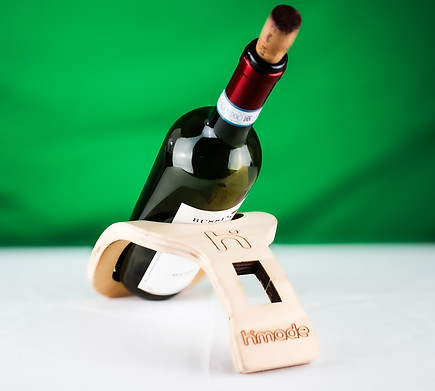



THE RESULTS OBTAINED THANKS TO THE BRAND
Cutting Edges has achieved the following results thanks to the HiMade brand;
Diversification of production
Economic savings for wood disposal, gone from 35 tons per year to about 15 with the declared goal of reaching 1 ton in 2025.
Increase in turnover and profits
To date, the economic advantage “cuba” a few tens of thousands of euros since the carpentry has only started a few weeks ago, it should be considered that the innovation introduced is generating strong interest. A project regarding the remodeling of 60 hotel rooms and the supply of over 80,000 gadgets for a reference brand is being defined.
With the Himade project we can pursue the company's mission, "to develop Functional Circular Economy projects to safeguard the Environment and the future of new generations". This is the real benefit.!
Replicating the model globally will generate unquantifiable economic and social benefits, the impact that will be generated will be the result of this innovative business model.



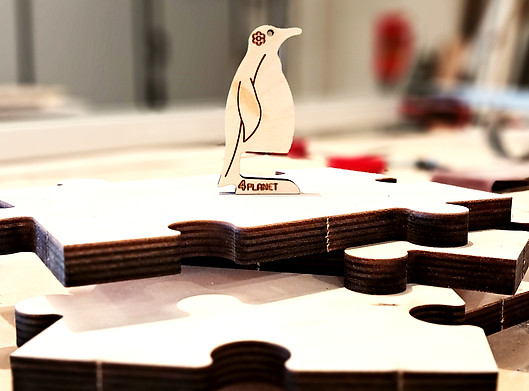